BETTER INSIGHTS
Data science
C-Job operates at the forefront of innovation, using data science techniques to drive better ship design. Our in-house developed tools, processes and algorithms convert data into insights, validate the performance of designs, and optimize vessels to meet their operational goals.
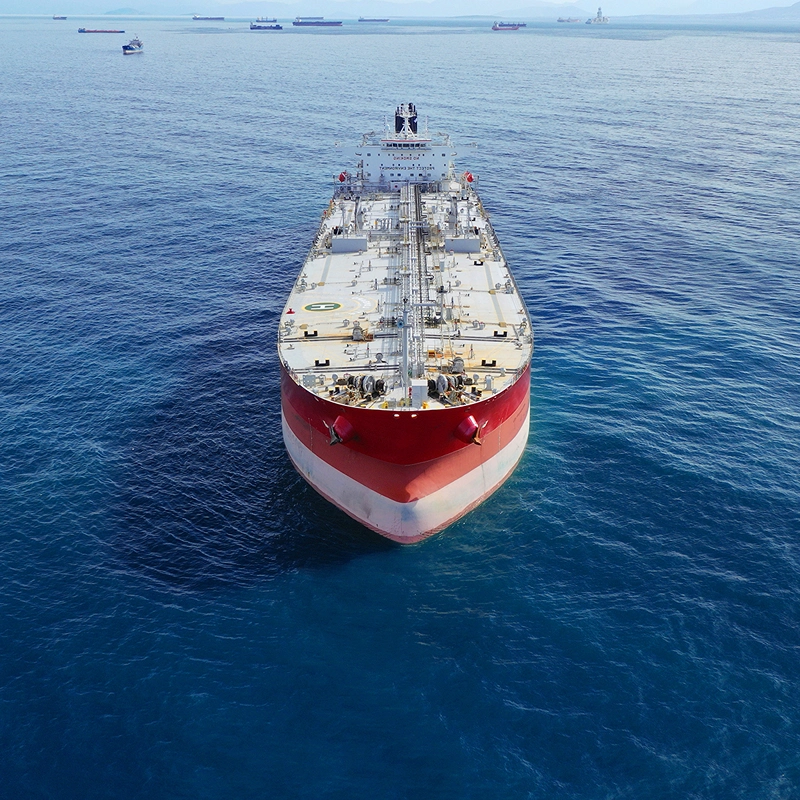
Speeding the design process and decision making
Depending on the requirement, C-Job’s data science teams will use data shared from your vessel, and/or other comparable vessels, to examine variables such as main dimensions, emissions, engine performance, mission equipment, hull stress and resistance, and operational profile.
We use insights from this real-life data to support the ship design process and analyze everything from installed engine power to hull lines and expected fuel consumption. Our naval architects and engineers can quickly see how design changes impact vessel design and performance, to fine tune your ship to meet operational and business goals.
Hull shape optimization
C-Job has carried out detailed research into optimizing ship design through the use of optimization algorithms. The process enables a parametrized vessel to be analyzed across all dependencies including decision variables, constraints and objectives.
Our initial research into Accelerated Concept Design used genetic algorithms to optimize the classical design spiral. C-Job has since improved its proprietary algorithm to perform accelerations of sections of the design spiral such as hull shape optimization. This generates new hull shape parameters which are automatically modelled on a 3D platform before being analyzed afresh by the algorithm. Our naval architects then analyze the data to choose the optimum design. Hull shape optimization is typically performed at the concept design stage, but can equally be used on vessels already in operation.
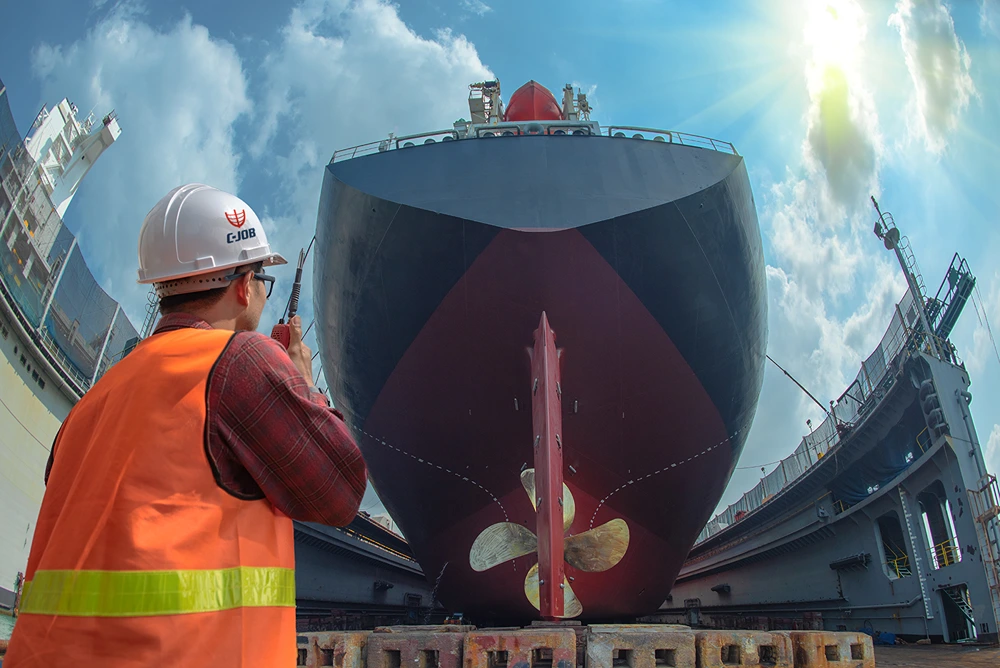
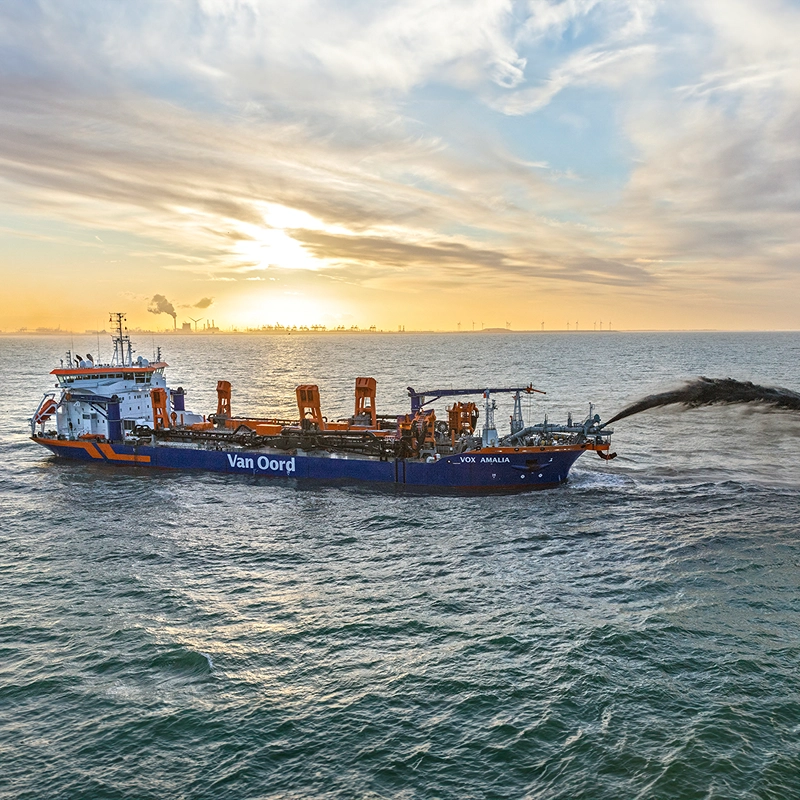
Operational profile analysis
One of the most important phases in vessel design is the beginning of the design process, when assumptions are made, critical decisions are taken, and the majority of budget is allocated.
C-Job researchers wanted to develop a more accurate way to validate early assumptions which have fundamental impact on a vessel’s design, such as: What exact speed are we designing for? What dimensions of mission equipment are required for my vessel’s operations? And is the design spiral taking the right direction?
It led us to undertake a new branch of research: operational profile analysis, which brings computer science and naval architecture together. An operational profile analysis gathers data including location, speed, course and heading, and marine environment data such as weather conditions. The analysis empowers our naval architects and engineers to make data-driven design choices, and validate assumptions for our customers.
More about C-Job
Our R&D work has contributed to a ripple effect, as the impact of our vessel designs and technical solutions continues to spread. Discover how we are empowering clients to build better ships, as we propel the maritime industry towards a more sustainable future.